一、多工位冷镦機各部件的性能要求
(1) 曲軸與機體、沖擊連杆的連接均采用高耐磨合金銅瓦連接,承載力大,使用壽命長,維修成本低。
(2) 機體采用添加合金的球鐵鑄造而成,抗拉強度高,耐磨性好。
(3) 采用二級齒輪傳動系統,傳動效率高,傳動力矩大。
(4) 配備氣動離合刹車器,降低電機功率能耗。
(5) 切料系統采用導闆驅動切刀杆,導闆往複運動,切斷力直線傳送,力大穩定且動态平衡性好。
(6) 挾鉗系統可以翻轉或平移,利于成型工藝安排。
(7) 配備變頻調速裝置,可在一定範圍内無極調速。
(8) 配備故障檢出器及安全保護裝置,設備故障時自動停機,給予設備和工模具最大保護。
(9) 送料箱安裝止推裝置,提高送料精度。
(10) 潤滑系統油路設計簡潔高效,在保證循環過濾的基礎上能有效起到保護沖棒和工件的作用。
二、工件原材料的選用
(1) 原材料必須進行球化退火處理,其材料金相組織爲球狀珠光體。
(2) 爲了盡可能減少材料的開裂傾向,提高模具使用壽命還要求冷拔料有盡可能低的硬度,以提高塑性。
(3) 原材料的尺寸精度一般應根據産品的具體要求及工藝情況而定,多工位冷镦機一般來說對于縮徑和強縮尺寸精度要求低一些。
(4) 原材料的表面質量要求有潤滑薄膜呈無光澤的暗色,同時表面不得有劃痕、折疊、裂紋、拉毛、鏽蝕、氧化皮及凹坑麻點等缺陷。
(5) 要求原料半徑方向脫碳層總厚度不超過原材料直徑的1%。
(6) 爲了保證冷成形時的切斷質量,要求原料具有表面較硬而心部較軟的狀态。
(7) 原料應進行冷镦試驗,由于冷作硬化使變形抗力增加。要求材料對冷作硬化的敏感性越低越好。
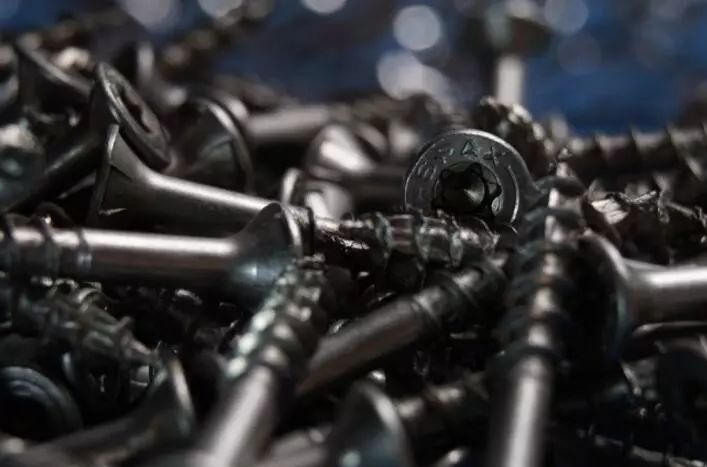
三、冷镦成型油的選用
(1) 具有優良的極壓潤滑性能,耐高溫性能、極壓抗磨性 、防鏽性及高溫抗氧化安定性能。提高加工件的精度和光潔度,能防止模具燒結,滿足标準件及非标件的多工位成型加工,能完全勝任冷镦不鏽鋼工件加工。
(2) 可以将油煙以及 "漂泊霧”減少到最低限度,滿足含強縮模的多模沖床加工螺帽之嚴格要求。
(3) 對變型量比較大的産品有很好的加工性能,如空心、高強度螺栓、套筒、不鏽鋼空心、半空心鉚釘等的成型加工。
(4) 能有效保護沖棒(沖針)及模具,延長使用壽命,降低綜合成本。
(5) 散熱效果好,避免了冷成型過程中工件及模具局部溫度過高。
(6) 高耐溫性能好,不易産生油泥。低氣味、低煙霧,保護操作環境。
(7) 具有一定的防鏽性,能滿足加工過程工序間防鏽要求。
(8) 能滿足苛刻的冷镦不鏽鋼成型加工及大變型量的碳鋼成型加工。
四、操作多工位冷镦機的注意事項
1、工作前做到:
(1) 檢查刀闆、切料刀杆、沖頭、凹模等應完好無崩裂,安裝正确緊固牢靠。
(2) 調正切斷機構後必須檢查與凹模夾之間的間隙,嚴禁不經檢查就開動設備。
(3) 在切料刀杆已折的情況下,必須把凸輪槽中的滾輪取出後方可點動設備。
(4) 認真檢查設備安全防護裝置是否完好,防止劇烈振動而松脫造成故障。
(5) 檢查冷镦機潤滑冷卻系統油路是否通暢,如有異物應立即清理,冷镦成型油不足時應及時添加。
2、工作中做到:
(1) 開動設備時隻有在斷開進料裝置的情況下,才準開動主電動機帶動飛輪回轉。隻有等待飛輪全速後才準接通進料裝置。停止設備時,應先斷開進料裝置再停主電動機。
(2) 不準将滑塊停在"死點"的位置上,如滑塊停在"死點"上時,隻準用人工盤動飛輪的方法來糾正,不準開動設備。
(3) 加工的棒料或盤料一定要清潔,料頭毛刺要磨掉,不準使有扁料。
(4) 經常注意盤料架的工作情況,發現混亂應立即停車。盤料加工到快完時,應将料尾從盤架上脫出。
3、工作後做到:
(1) 依次關閉多工位冷镦機各系統,然後切斷電源。
(2) 将冷镦機擦拭幹淨,工作台面塗防鏽油。
(3) 每次運行或維護之後做好記錄。
(4) 發生故障必須立即停多工位冷镦,查明原因消除隐患。